Occupational Health and Safety
Occupational Health and Safety

Since 2022, Chroma has been implementing the ISO 45001:2018 Occupational Health and Safety Management System at its headquarters (including Huaya Plant), Hsinchu Branch, and Kaohsiung Branch in accordance with the regulations of the Occupational Safety and Health Act. This system covers all employees, as well as non-employees whose work is controlled by the organization (including contractors). After successfully obtaining the ISO 45001:2018 Occupational Health and Safety Management System verification in 2023, the Company plans to undergo external reverification every three years thereafter to ensure the effective operation of the occupational health and safety management system.
Hazard Identification, Risk Assessment
Chroma has adopted a preventive approach to prioritize the safety and health of its workers. In 2023, we conducted a comprehensive risk assessment and initiated a digital transformation across all plants. This ensured compliance with occupational safety, environmental protection, human resources, and facility management regulations. We also compiled a comprehensive list of chemicals used across all plants to identify health hazards and determine the necessary monitoring and control
measures for hazardous chemicals and prioritized substances.
The Safety & Health Center and the Occupational Safety and Health Management System promotion team conducts annual hazard identification and risk assessment for all personnel under organizational control (including employees, contractors, and visitors) based on the “Occupational Safety and Health Hazard Identification and Risk Assessment Management Procedures.” We prioritize and control unacceptable risks according to the assessment results. Employees can proactively report identified hazards in the workplace to the Safety & Health Center by email or phone to contribute to our goal of zero accidents and zero hazards through joint efforts by labor and management.
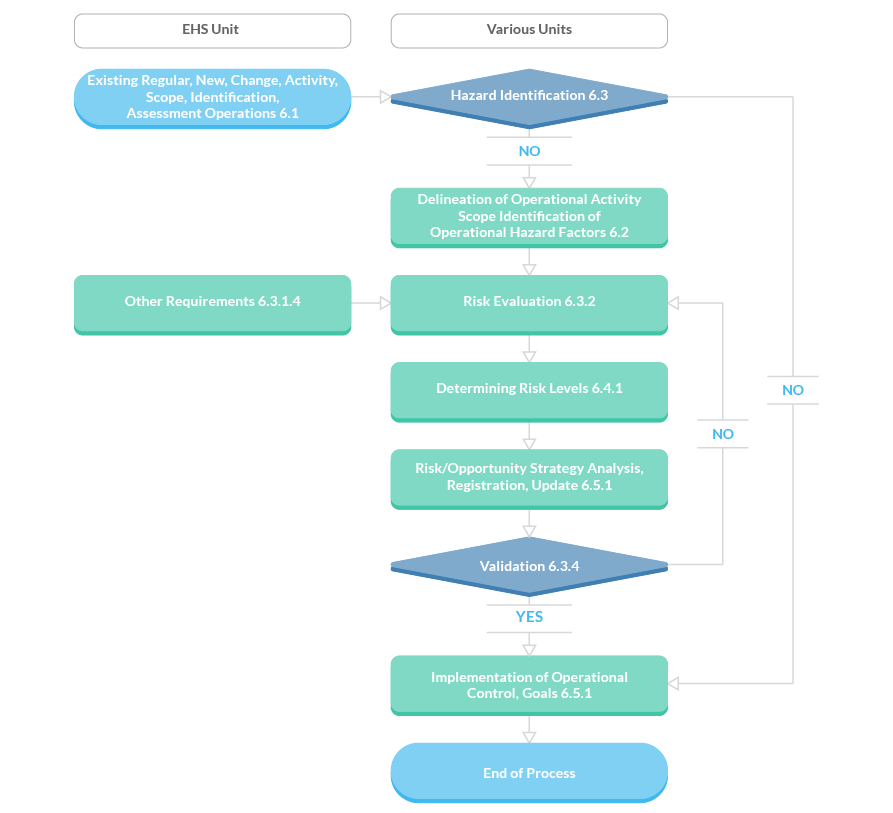
Hazard Identification and Risk Assessment Targets and Scope
: Personnel under organizational control: This includes company employees and contractor workers (cleaning, security, catering staff, etc.).
Hazard Identification and Risk Assessment Process
Identify potential hazards and determine their risk levels for the work environment, processes, activities, products, and services, and prioritize control measures for unacceptable risks.
Contractor workers undergo hazard identification and risk assessment, with risks and control measures communicated during pre-job or toolbox meetings.
Control measures are implemented from the source through change management when there is a need for new equipment procurement or process changes. This ensures the safety and health of personnel and the plant. These measures include safety assessments before the acquisition of new machinery, the addition of safety protection measures, and the selection of less hazardous chemicals to replace highly hazardous ones.
Response Measures for Immediate Hazards
: To ensure labor safety in the factory, it is made clear in the Chroma education and training courses that should there be immediate danger or serious accident in the workplace, the person in charge should immediately order the workers to stop the operation, or the workers themselves should immediately stop, and evacuate to a safe place. There will be no penalty of any kind for such action.
Operational Control / Action Measures (Hierarchical Control Mechanism)
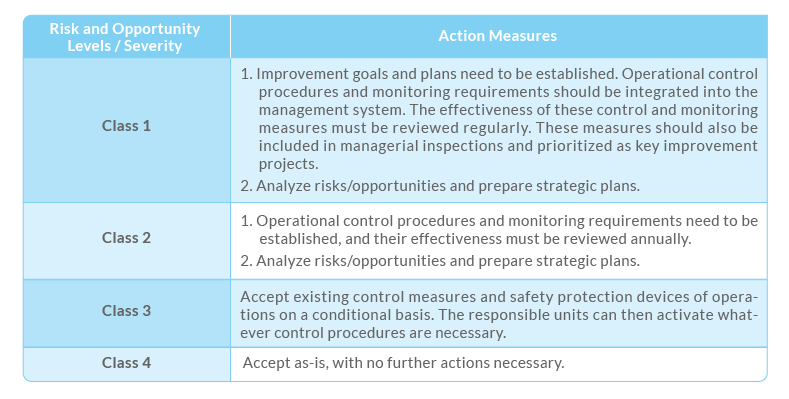
Accident Investigation
(1) Commuting Accidents: Incidents occurring during employee commute, including traffic accidents and other unforeseen accidents.
(2) Near Miss Incidents: Events that cause no injuries or fatalities, but which induce fear in personnel.
(3) Major Accidents:
① Incidents resulting in death, involving three or more injured persons, or involving one or more persons who require hospitalization.
② Fire incidents
③ Accidents reported by the mass media.
(4) Severe Injuries: Injuries causing serious damage, resulting in loss of function in some organs (such as the loss of a limb, sight or hearing)
(5) Minor Injuries: Occupational accidents that do not result in lost workdays.
Accident reporting and statistical analysis:
(1) The EHS unit must compile and retain monthly statistics on the FR (Disabling Injury Frequency Rate) and SR (Disabling Injury Severity Rate).
(2) The EHS Unit must report occupational injury statistics to the labor inspection authorities by the 10th of each month in accordance with the Occupational Safety and Health Act.
(3) In the event of a major accident, the EHS must notify the labor inspection authorities within 8 hours.
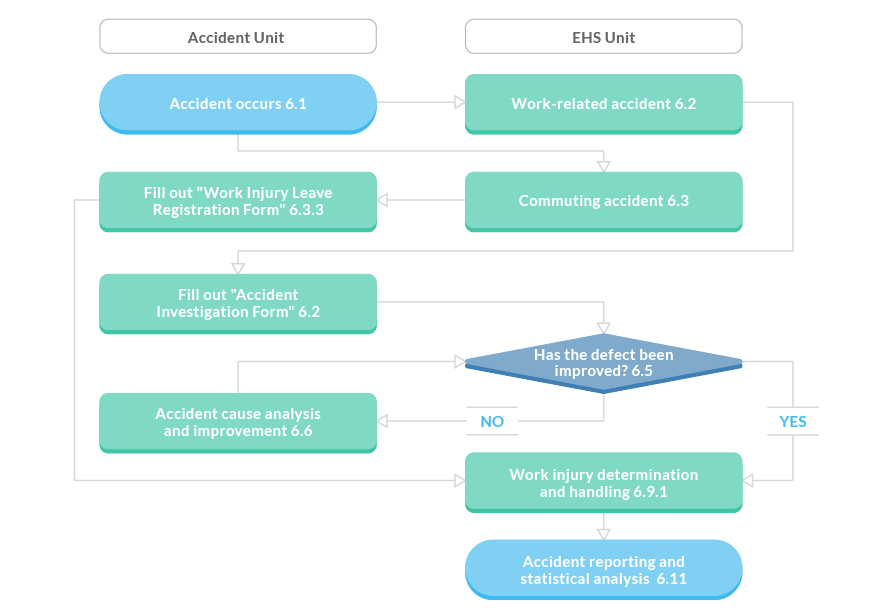
The occupational injury and public injury statistics for the headquarters and various plants from 2021 to 2023 are summarized in the table below
Note: The occupational injuries in the statistics are determined based on the accidents occurring within the plants (excluding commuting accidents).
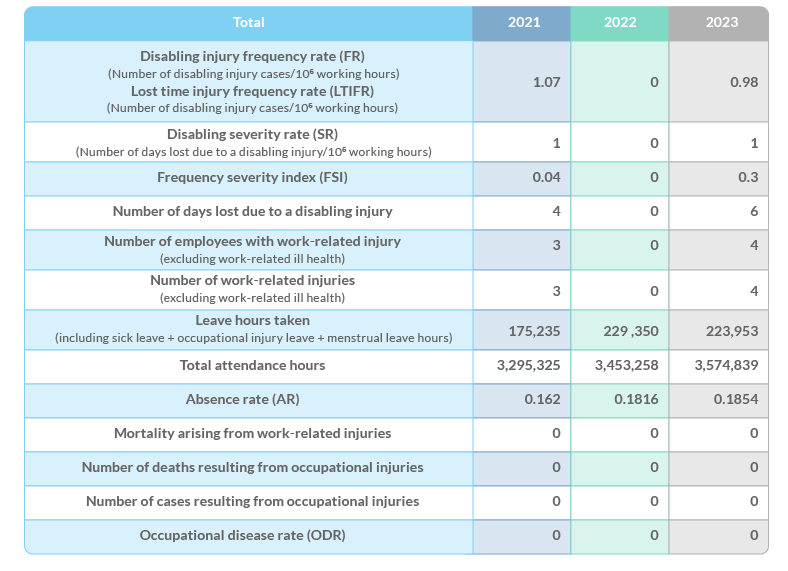
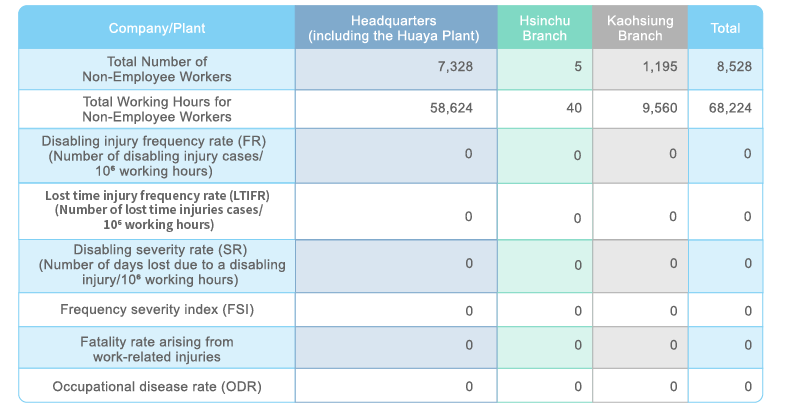
Method of calculation:
1. The total working hours for non-employee workers = the total number of non-employee workers x 8 hours.
2. Disablement Frequency Rate (FR) = Number of disabling injuries x 106 / total working hours.
3. Lost time injury frequency Rate (LTIFR) = Number of lost time injuries x 106 / total working hours.
4. Disablement Severity Rate SR (SR) = Number of days lost due to a disabling injury x 106 / total working hours.
5. Frequency severity indicator = √(FR*SR/1000).
6. Absence rate (AR) = Number of days for sick or personal leave / Total number of working days x 100%.
7. Occupational disease rate (ODR) = Total number of employees with occupational disease x 106 / Total number of working hours.
Occupational Health and Safety Education
Chroma adheres strictly to Occupational Safety and Health Education and Training Regulations and related guidelines to ensure that every worker is well-versed in the relevant laws and the company’s safety and health management mechanisms. The Company provides occupational safety and health education and training for all new employees and assesses the effectiveness of the training through post-training tests. The Company also conducts periodic safety and health training courses for current employees to strengthen the concept of fundamental safety and health and encourage its practical application. Furthermore, all occupational safety and health education training sessions are conducted during working hours so that employees do not suffer pay cuts, salary reductions, or leave deductions for participation. In 2023, 2,128 employees completed health and safety-related training sessions, and the collective training amounted to 3,305 hours.
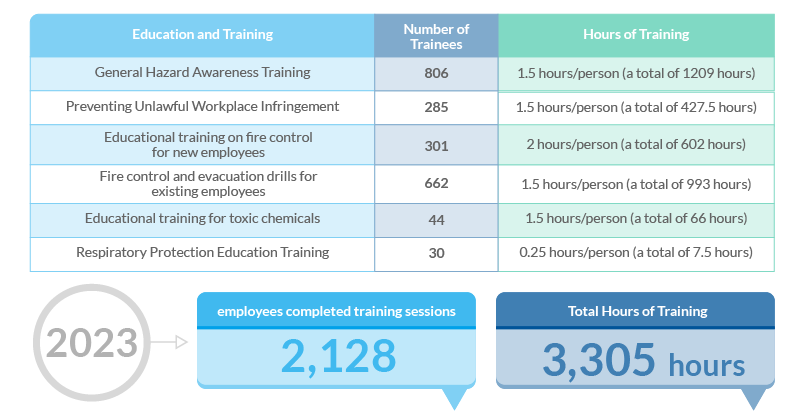
Chroma considers contractors to be important partners, and managing them is a complex yet essential task to ensure their safety at work. Controlling the entry and exit of personnel is important, as contractors are not company employees and may lack adequate safety awareness. To address this concern, in addition to daily toolbox meetings that include safety briefings, all first-time contractors receive hazard awareness training conducted by the Safety & Health Center to ensure they are familiar with all plant regulations and procedures.
In addition, when there are different contractors working on the same construction project at the same time and location, agreement needs to be made to ensure cooperation between them and to guarantee that those in charge handle any non-compliance and maintain enough vigilance to ensure proper compliance with the regulations. There were zero accidents involving contractors at Chroma in 2023. However, we must not be complacent and should aim for zero occupational incidents, not only among our contractors, but among all employees.
Prevention and Mitigation of Occupational Health and Safety Impacts Directly Linked by Business Relationships
In addition to compliance with government regulations and company operating standards, automatic self-inspections are conducted to ensure the safety of workers and the plant. The Safety & Health Center staff also perform routine safety audits and random safety checks on contractors. Chroma began implementing the ISO 45001:2018 Occupational Health and Safety Management System in 2022 and received ISO 45001 certification in 2023. The Safety & Health Center continues to carry out periodic inspections and makes improvements from time to time. Medical professionals also make on-site visits and provide suggestions for enhancing vario us work activities. These efforts have already yielded positive results.
Worker Participation, Consultation, and Communication
The Company has formulated a “Consultation and Communication Management Procedure”. This facilitates the internal agreement on the ESH management system and other management mechanisms. It also establishes commitment and effective two-way communication channels for employees and related external organizations with respect to ESH and the other management mechanisms. Consultation with the workers about safety and health is necessary whenever changes are made to any workplace. The arrangement of the consultation must be documented and meeting notes and minutes should be taken. Stakeholders must also be informed of the changes.
Employees are Chroma’s most valuable asset, and their health and safety are of vital importance. Chroma has established an “Occupational Safety and Health Committee” to ensure that employees work in a healthy and safe environment and to implement safety and health policies. This committee has 16 members and includes occupational safety and health personnel, relevant department heads, and labor representatives. There are six labor representatives, representing 38% of the committee. This exceeds the legal requirement of one-third representation. The committee convenes once every three months and makes recommendations on the following items ▶
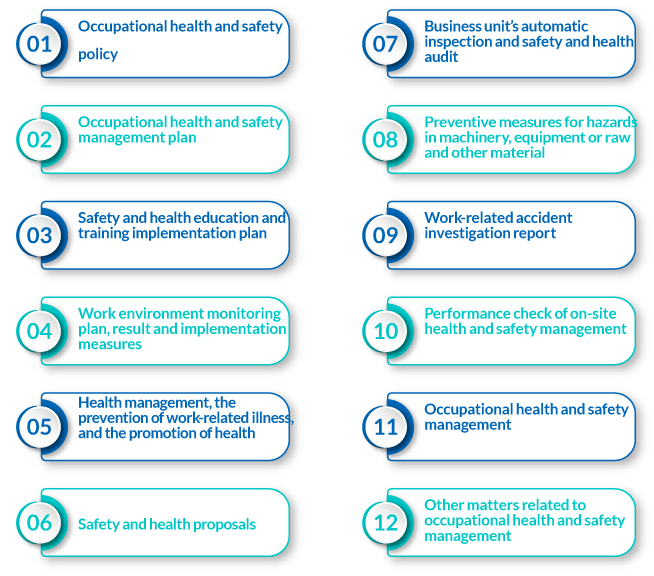
In 2023, the committee members proposed seven items for discussion. Of these, five were implemented and improved within the same year, while the remaining two are scheduled for implementation in the following year.
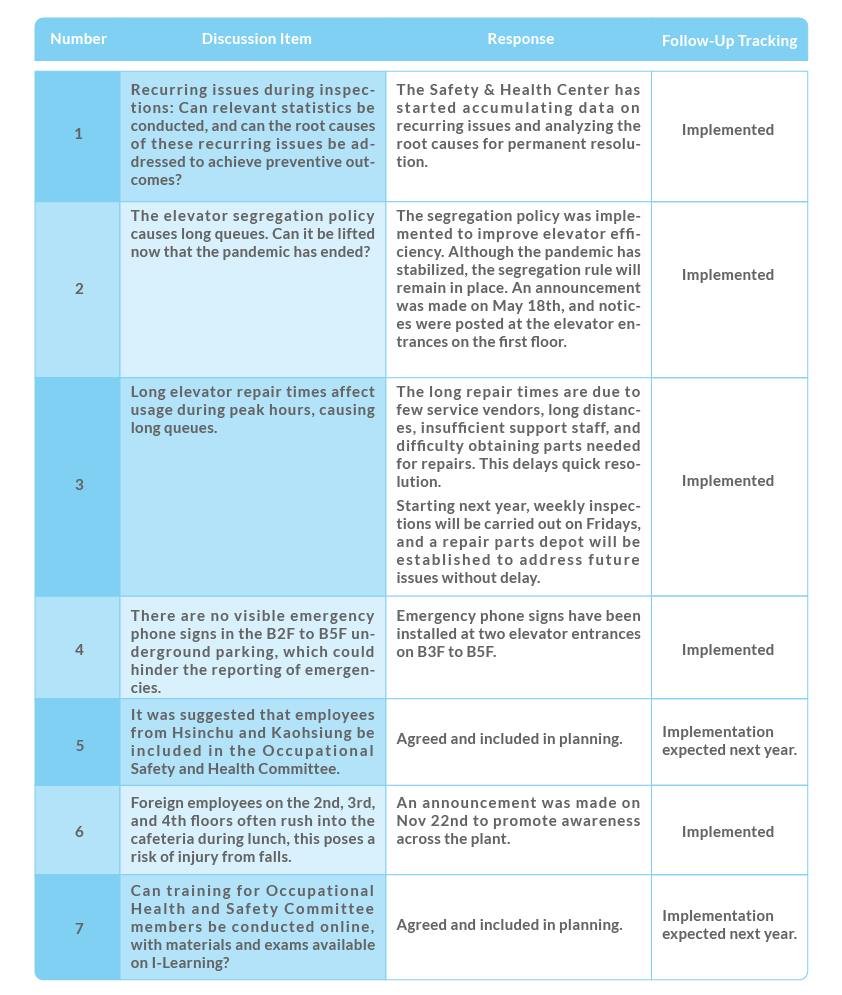
38% of the total members of the Occupational Health and Safety Committee are labor representatives and the composition is as follows.
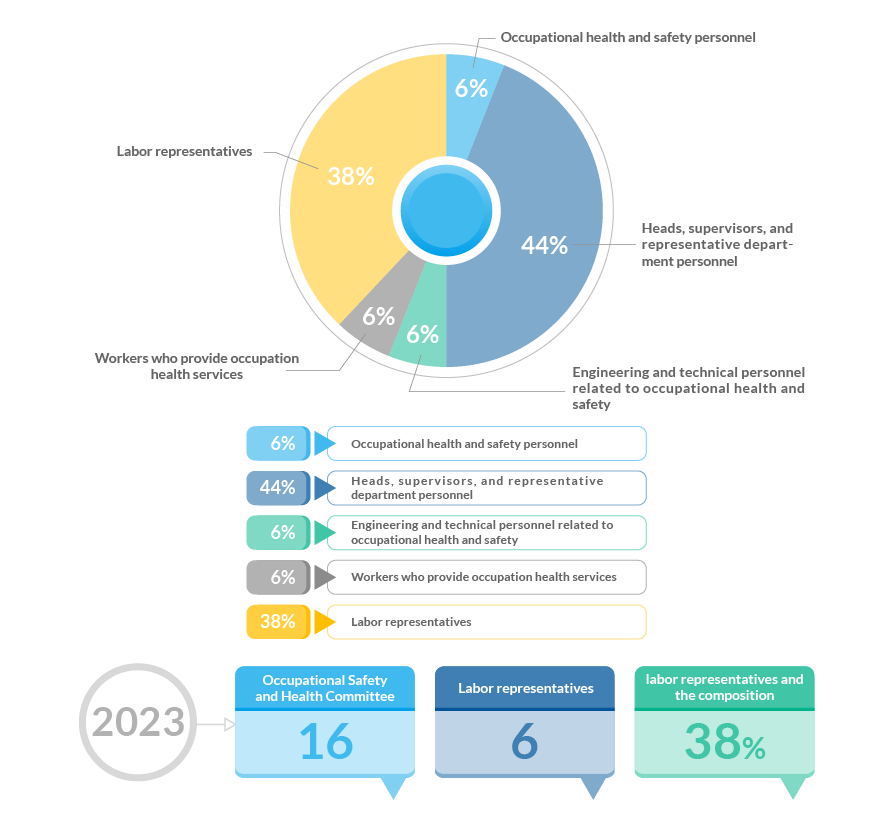