Risk Management
The Board of Directors is the highest decision-making unit for the Company's risk control, and directly supervises the Company's risk governance structure. In response to changes in the global economic environment and sustainable risks, the Company has established a complete risk management organizational structure and implementation promotion levels to identify and grasp the relevant risks that may affect the sustainable development of the Company based on the three major aspects of economy (including corporate governance), environment and society. Through relevant management strategies and response measures such as risk transfer, reduction and avoidance, possible risks are minimized and even transformed into operating opportunities.
Chroma defines various risks in accordance with the "Organizational Context Analysis and Risk Management Procedure" established by the Operation Management Center and the Company's overall operating policy, and establishes a risk management mechanism for early identification, accurate measurement, effective supervision and strict control. It prevents possible losses within the acceptable risk range, continuously adjusts and improves the best risk management practices based on changes in the internal and external environment, in order to protect the interests of employees, shareholders, partners and customers, increase the Company's value, and achieve the principle of optimizing the Company's resource allocation.
The corporate risk management process consists of three steps:
Step 1 Risk Category Identification

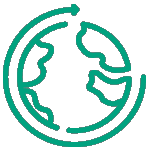
Environment
1.1.1 Risks related to the management of greenhouse gas emissions, carbon credits, and energy management in response to climate change and natural disasters; and risks of compliance with international and local environmental laws and regulations, such as the management of air, water, waste, toxic substances, noise emissions, or envir onmental impact assessment requirements.
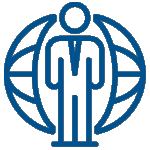
Social
2.1.1 Operational aspect: includes risks t o the Company caused by occupational health and safety, chemical management, safety protection and emergency response, and other risks resulting from improper or erroneous human management and operations.
2.1.2 Workplace environment aspect: includes risks related to issues of a saf e working environment for employees or contractors.
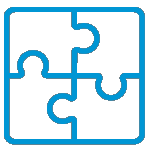
Economic (Including corporate governance)
3.1.1 Political and economic aspect: includes risks to the Company's finances or business caused by domestic and international political, economic, and regulatory factors.
3.1.2 Industry aspect: includes risks to the Company's finances or business caused by changes in domestic and international technology and industry trends. Chinese competitors are rapidly launching products with highly competitive specifications and prices, not only in the Chinese mark et but also expanding into European and American overseas markets.
3.1.3 Financial aspect: includes risks of changes in value of the Company's financial assets or liabilities (including assets and liabilities bo th on and off the balance sheet) caused by fluctuations in market risk factors (interest rates, exchange rates, stock prices, commodity prices, and electricity prices), resulting in various losses.
Step 2 Risk evaluation

Step 3 Establish risk control measures

Risk Type
1.1 Environmental Risks
Risk control measures
- Continuously improve processes to reduce carbon emissions in response to environmental protection issues.
- Demonstrate the outcome of technology innovation on outstanding performance and the function of new products and implement green design at all stages of the product life cycle to reduce environmental impact and realize responsible production and consumption.
- Set a goal of net-zero emissions by 2050, starting with assessments of production and office environments, improvements in production processes, and green product design, gradually move from low carbon to net-zero.
Risk Type
2.1 Workplace Hazard Risks
Risk control measures
- Comply with relevant regulatory requirements and establish various operational management guidelines.
- The Occupational Safety and Health Committee regularly reviews compliance with environmental/occupational safety regulations.
Risk Type
2.2 Human Resource Risks
Risk control measures
- Conduct regular manpower inventory and audits.
- Plan and implement employee education, training, and development programs.
- Design competitive compensation and employee benefit measures.
- Comprehensive training and local talent development programs.
Risk Type
3.1 Market Risks, 3.2 Operational Risks, 3.3 Investment Risks, 3.4 Regulatory Compliance Risk
Risk control measures
- In recent years, there has been an exponential growth in the electric vehicle (EV) industry, particularly in the manufacturing of automotive electronic components, batteries, and charging stations. Safety and durability are vital in the automotive electronics sector, while climate change concerns have spurred measures to reduce carbon emissions and adopt new energy sources. Additionally, the demand for products in this industry has been further driven by the growing interest in solar and wind power, among other renewable energy sources.
- Rigorous quality requirements necessitate more complex and extensive testing equipment, and improving testing quality and speed is a key issue in the development of the instrument industry.
- Advanced processes in the semiconductor industry continue to lead the development of ICT industries, and applications in emerging technologies continue to expand.
- Semiconductor manufacturing has been a driving force behind the overall advancement of the industry. The Company has consistently prioritized the development of semiconductor equipment, recognizing it as a key area of focus. The company continues to develop cutting-edge semiconductor testing equipment by the integration of optical, electrical, thermal, and automation software technologies. This strategic initiative is aimed at expanding the Company's presence in advanced manufacturing processes in the years to come.
- Every year, substantial resources are invested in research and development, and through investments in companies with unique technologies, the Company ensures leadership in key technologies. Chroma' s robust integration capabilities across optical technology, mechanics, electronics, thermal control, and software contribute to its competitive edge and facilitate growth. These efforts ultimately align with the achievement of sustainable development.