Environmental sustainability management
Energy conservation, carbon reduction, and the lowering of environmental impact
Environmental sustainability management

Chroma has obtained ISO 14001:2015 certification for its environmental management system, covering all four of its plants (100% coverage). Through the PDCA (Plan-Do-Check-Act) management cycle, operations related to all pollution sources are standardized and regulated by applicable laws to enhance environmental performance and strengthen the environmental management system.
To ensure the credibility of our greenhouse gas inventory data, we have also obtained third-party verification according to ISO 14064-1:2018. Climate change, green product design, pollution prevention and control, and comprehensive environmental protection are important aspects of the product life cycle that are taken into account. Others include product design, raw material supply, the manufacturing processes, factory operations, end products, post-sales services, and the legal and proper disposal of waste. Proper consideration of all these aspects will reduce the negative impact on climate change and environmental harm throughout the entire product life cycle.
In recent years, natural resources have rapidly diminished due to climate change and biodiversity loss. “Biodiversity” not only involves the richness of life on Earth, but also the ecological balance and aspects of the ecosystem such as climate regulation, water resources, soil fertility, agricultural production, and human health. In 2022, nations worldwide achieved consensus during the 15th Conference of the Parties to the Convention on Biological Diversity (COP15) to establish objectives and management directives for global biodiversity policies and initiatives by 2030 through the new Global Biodiversity Framework (GBF). Chroma recognizes the importance of restoring and conserving biodiversity. We are dedicated to protecting biodiversity during our production processes and minimizing damage to it, striving to achieve net positive impact. We firmly believe that sustainable business operations hinge not only on pursuing operational development and revenue growth but also on continuous innovation, constant enhancement, gradual implementation, and actively exerting a positive influence. Therefore, these commitments have been integrated into the environmental policy.
Energy Management and Resource Conservation

Electricity and fuel management
The Company mainly uses purchased electricity and fuels such as natural gas for the cafeteria, dormitory and health center; gasoline for company cars and diesel for generators.
Reference for conversion factors: MOEA Bureau of Energy - Heat Content of Energy Products (Updated on May 15, 2020)
- Electricity: 860,000 kcal/kWh
- Liquefied Petroleum Gas (LPG): 12,062 kcal/kg
- Natural Gas (NG): 9,000 kcal/m3
- Gasoline: 7,800 kcal/L
- Diesel Oil: 8,400 kcal/L、1 kcal =4,186 j
Note1: Calculated based on contracted capacity and power generation.
Note2: Renewable energy consumption data has been recorded since July 2022.
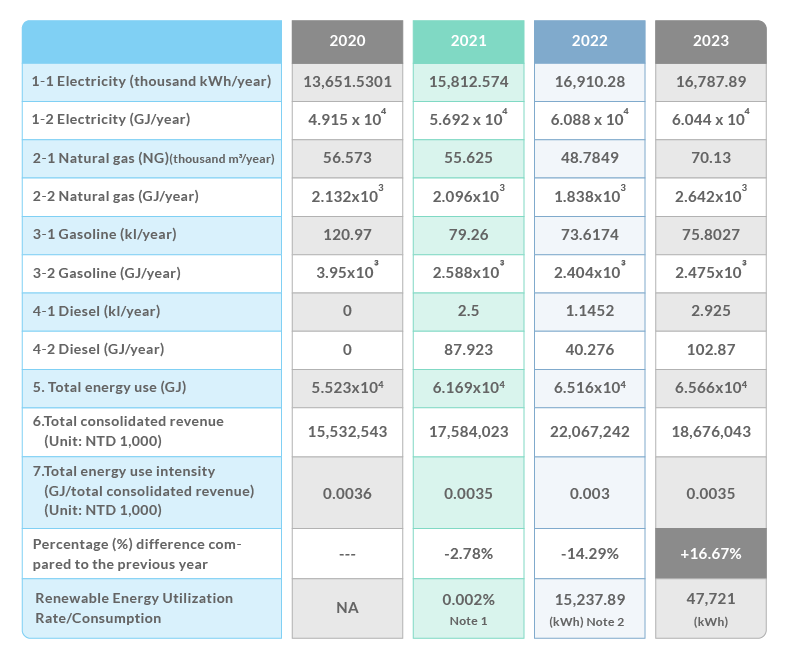
Water resource management
Chroma Headquarters (including the Huaya Plant), Hsinchu Branch, and Kaohsiung Branch are located in the Huaya Science Park, Hsinchu Science Park, and Nanzih Processing Zone, none of which are in environmental protection areas. The water supply for these facilities is 100% municipal tap water and is not from protected water sources. Chroma factory processes primarily involve assembly and testing and there is no significant demand for large amounts of water. Main water usage is for employee activities and facilities around the premises. Water is used for air conditioning, but has no noticeable impact on water resources or the ecological water environment. The generated domestic sewage is processed by appropriate sewage processing facilities or discharged directly into the sewage system pursuant to the law. Nevertheless, in addition to conserving electricity, we believe that water is also a precious Earth resource. Therefore, reducing water usage and enhancing water resource utilization are equally important tasks. To implement water resource management, the headquarters building has a rainwater harvesting system. After undergoing sedimentation treatment, the collected rainwater is utilized for gardening and irrigation purposes. This saves water and makes its use more efficient.
Water consumption and water use intensity at headquarters, the Huaya Plant and the Hsinchu and Kaohsiung Branches, over the past 3 years.
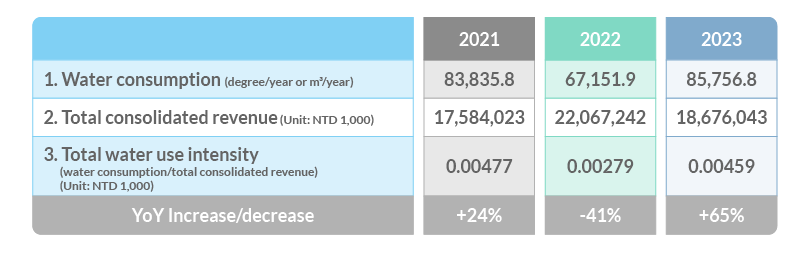
Total Water Withdrawal and Total Water Consumption
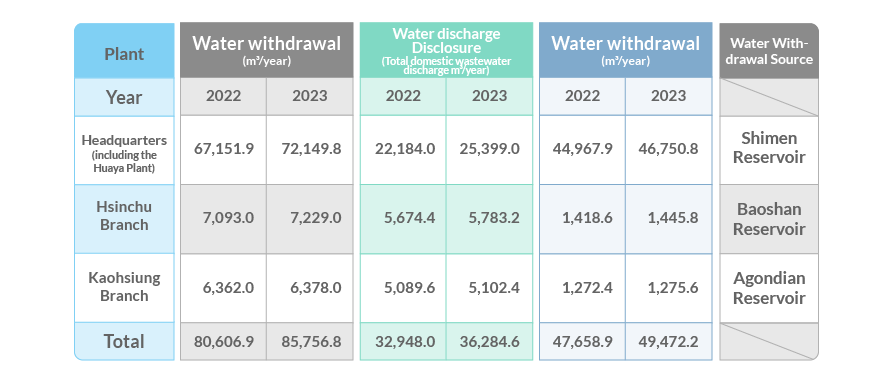
Energy conservation measures
We mainly use purchased electricity, and electricity conservation is a Company priority for carbon reduction. Various energy-saving measures have been implemented through the establishment of environmental health and safety objectives, including air conditioning energy efficiency improvements at headquarters (including the Huaya Plant), and the replacement of energy-efficient lighting fixtures at the Hsinchu and Kaohsiung branches. The most significant improvement was observed at the Kaohsiung branch.
In 2023, process improvements and smart production methods enhanced energy efficiency and carbon reduction. This resulted in a total carbon reduction of 1,696 tCO2e。
1. Reduce energy consumption due to aging processes
(1) Analyzing burn-in monitoring data and generating monthly analysis reports to promptly adjust burn-in operating hours, thereby reducing energy loss.
(2) Use energy-efficient equipment in the product aging process for power measurement and to monitor instrument products using smart monitoring which also reduces energy consumption.
(3) Utilizing product recycling capabilities for mutual power supply and burn-in loading to reduce electricity usage in aging processes. (Model 61815 & 62180D Series)
(4) Implementing a three-color light monitoring module at testing stations to record idle times and reduce electricity wastage.
(5) Installing flow monitoring devices on compressed air pipelin es and establishing data databases and monitoring pages to adjust settings based on monitoring data to save electricity.
2. Process Improvements
(1) Implement production environment monitoring to ensure process environmental quality (clean rooms, product aging rooms, optical product testing rooms).
(2) Introduce labor-saving equipment for product packaging operations, improve ergonomics, and reduce manual handling to ensure occupational safety.
(3) The SMT/DIP process has been enhanced through the introduction of intelligent electronic shelves, the establishment of automatic dispensing equipment, the evaluation and implementation of smart SMT storage, installation of DIP automatic soldering machines, and the implementation of full-process logistics production (processing -> plugging -> postsoldering). Improvements have also been made to the single-board testing fixtures in the 62XXX series, optimization of single-machine assembly and packaging times, optimization of system assembly methods, introduction of rail pressing fixtures, MOS automated testing fixtures, high-pressure isolation cover fixtures, manganese-copper semi-automatic grinding fixtures, and improvements in semiconductor and electromechanica l product processes.
3. Smart Production
(1) Analysis of Manufacturing Execution System (MES) data to monitor 8000 assembly hours and 1100 testing hours, enabling real-time adjustment of standard working hours to reduce product production costs.
(2) PCB automatic testing has been optimized to speed the tempo of production.
(3) Intelligent transformation of the whole machine and automation of system testing simplifies analysis.
(4) Optimization of full-machine testing hours.
GHG Management

The Company is in compliance with ISO 14064-1:2018 and is keeping track of the GHG emissions at headquarters and the branches using the inventory process. The Company is also using the GHG inventory system to develop feasible plans for future reduction of GHG emissions. To boost the validity of our GHG inventory information and report as well as the quality of the GHG inventory, an unbiased third-party verification organization has been commissioned to verify our inventory process (after an internal verification process has been completed) to ensure complete inventory procedures and optimal data quality.
The GHG emissions were calculated using the operational control method based on the GWP value as outlined in the IPCC’s Sixth Assessment Report. The seven emissions inventoried include CO2, CH4, N2O, CFC, PFCs, SF6 and NF3. The quantitative inventory can be divided into two parts:
- Scope 1 comprises direct GHG emissions, which include fixed, process, mobile and fugitive emissions.
- Scope 2 comprises indirect energy GHG emissions from purchased electricity.
As the ISO 14064-1:2018 standard was used as an inventory and quantification base, 2021 is the base year. To ensure effective and accurate monitoring of our GHG emissions, we used GHG intensity (tons of CO2e/total consolidated revenue (NTD 1,000) as a GHG management indicator.
The scope of the GHG inventory covers:
*Total GHG emissions for categories 1 and 2 from Headquarters and Huaya Plant from 2021 to 2023: (with 2021 as the base year)
(1) Headquarters: Chroma ATE Inc. (excluding the areas rented to DynaScan Technology Corp and Adivic Technology Co Ltd)
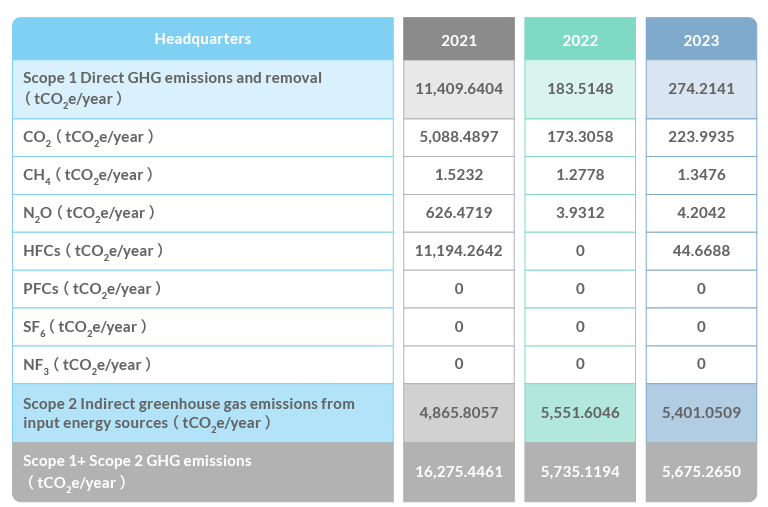
(2) Huaya Plant
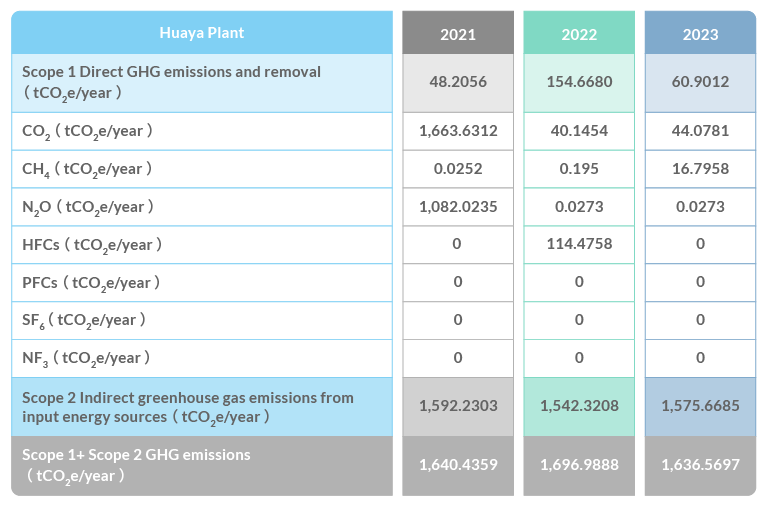
(3) Hsinchu Branch (excluding the areas rented to the Testar Electronics Corp)
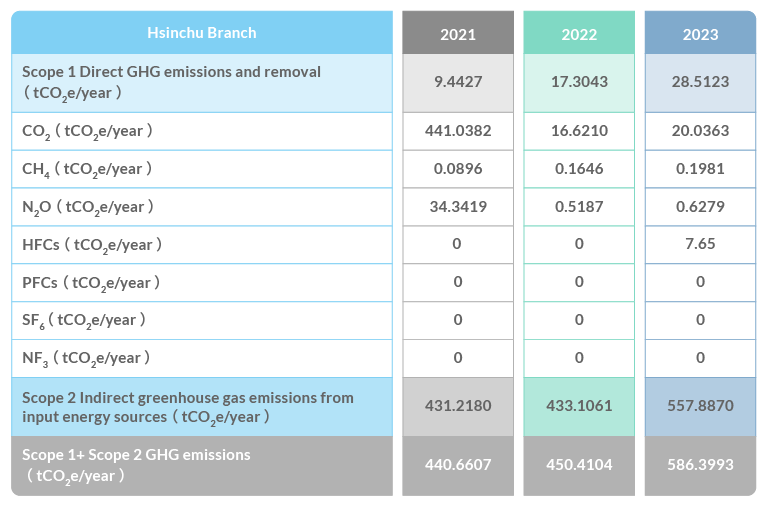
(4) Kaohsiung Branch
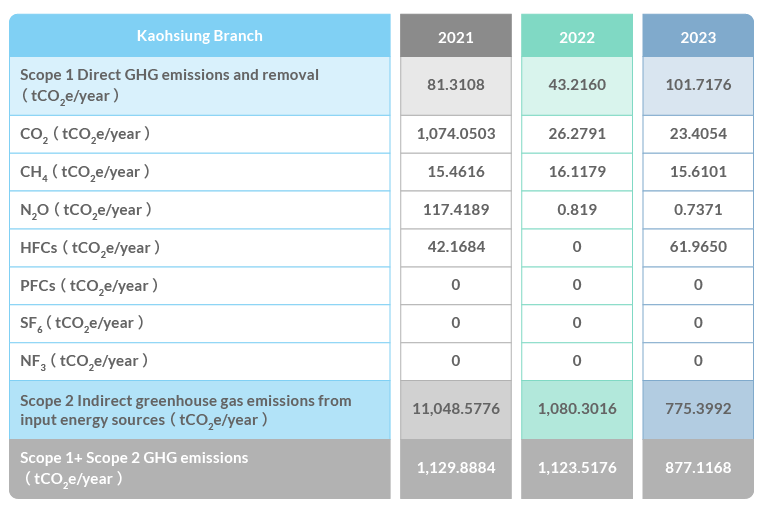
GHG emissions for Scope 1 and 2 from 2021 to 2023
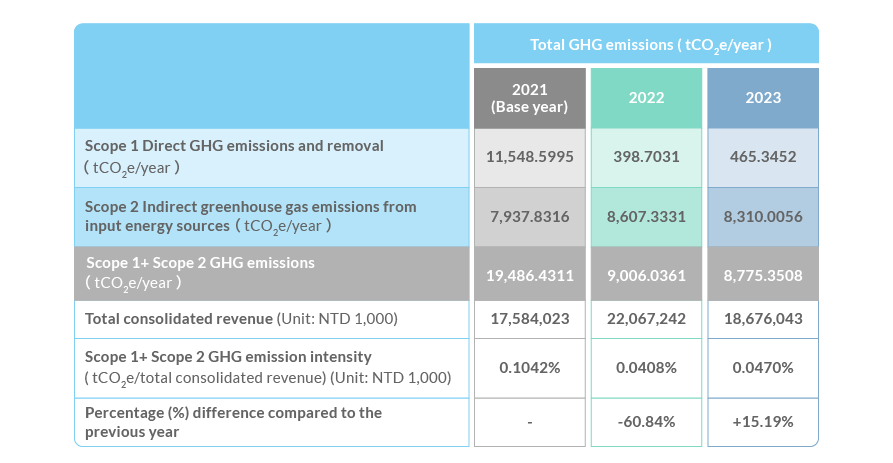
As Chroma ATE Inc. was relocated at the end of 2020, the emissions from refrigerant were calculated based on the amount of filled refrigerant. Thus, the Scope 1 emissions were much more than the Scope 2 emissions. As a result, the GHG emission intensity in 2023 decreased by 54.89% compared to the base year of 2021, but increased by 15.19% compared to 2022.
In 2023, the emissions of categories 3 to 6, which include other indirect greenhouse gases, were quantified. This quantification focused on emissions from the disposal of solid and liquid waste. Additionally, emissions from employee shuttle buses were quantified for this year.
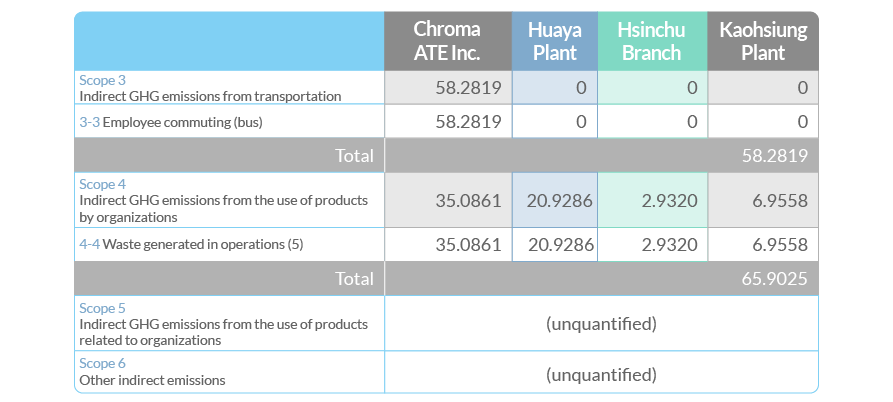
Waste Management

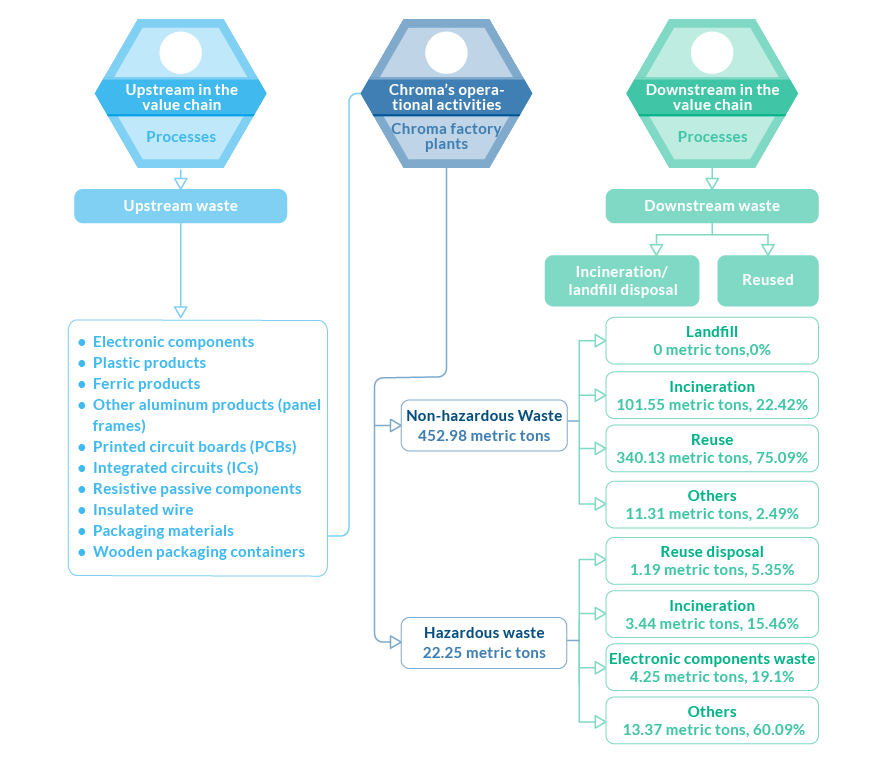
Non-hazardous waste
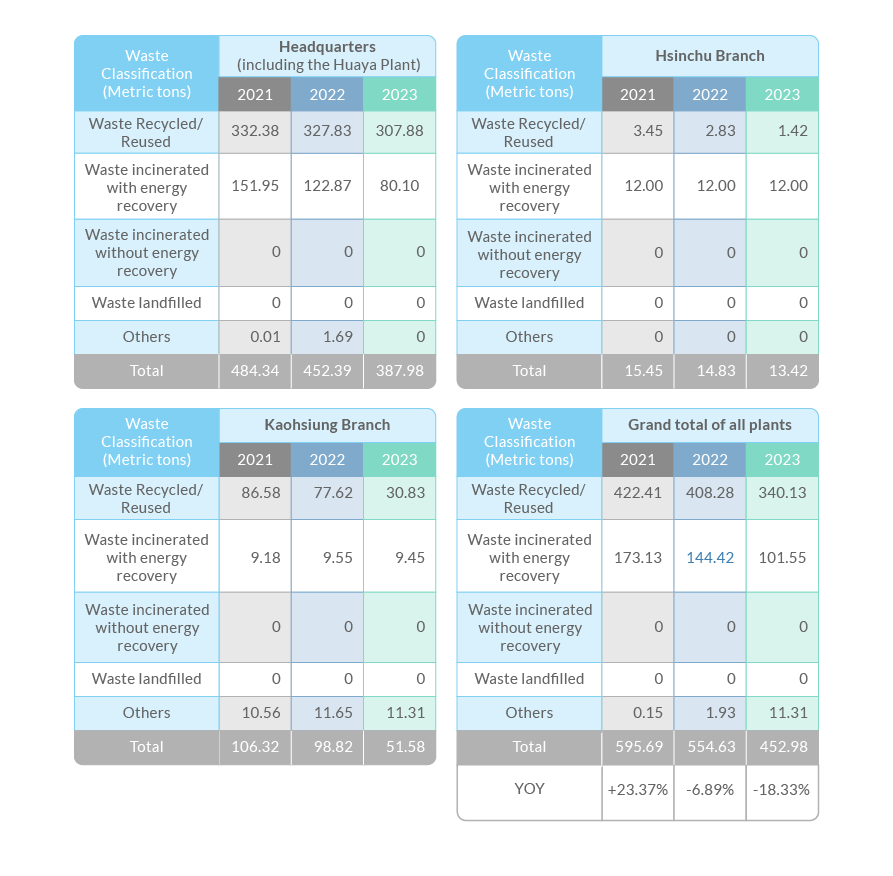
Hazardous waste
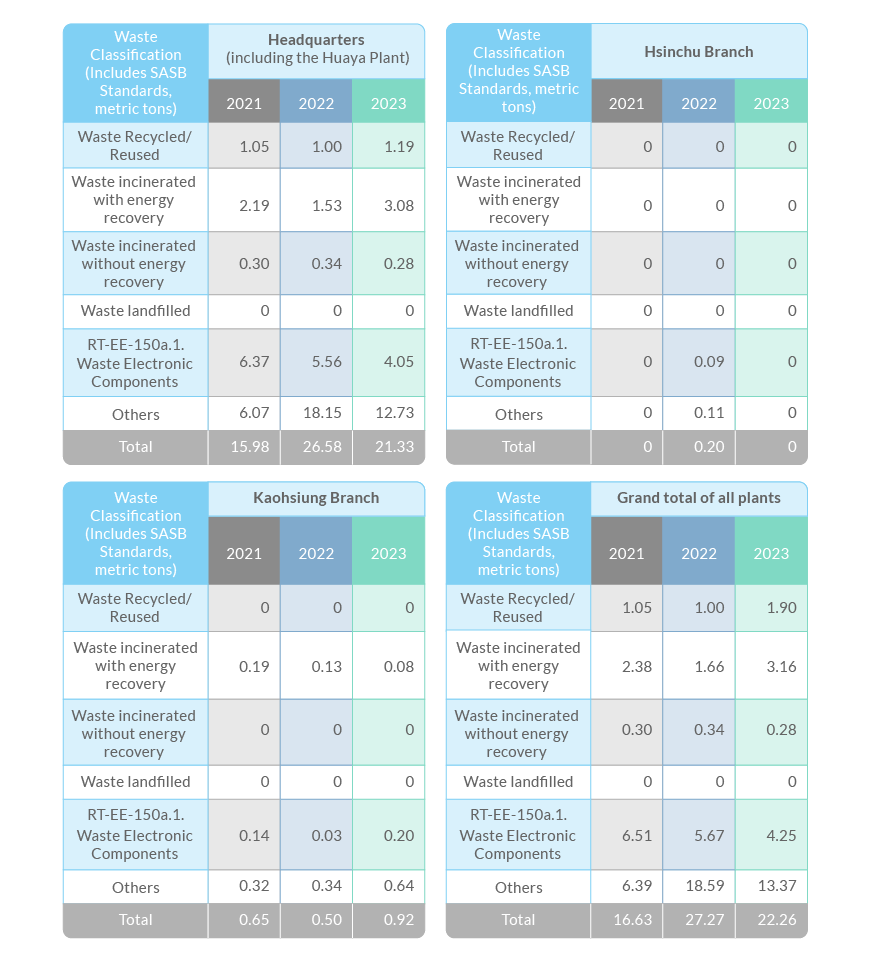
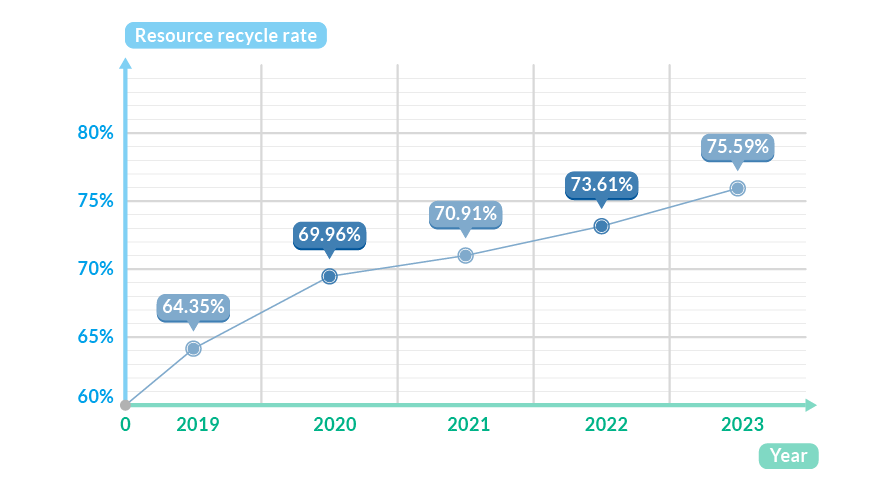
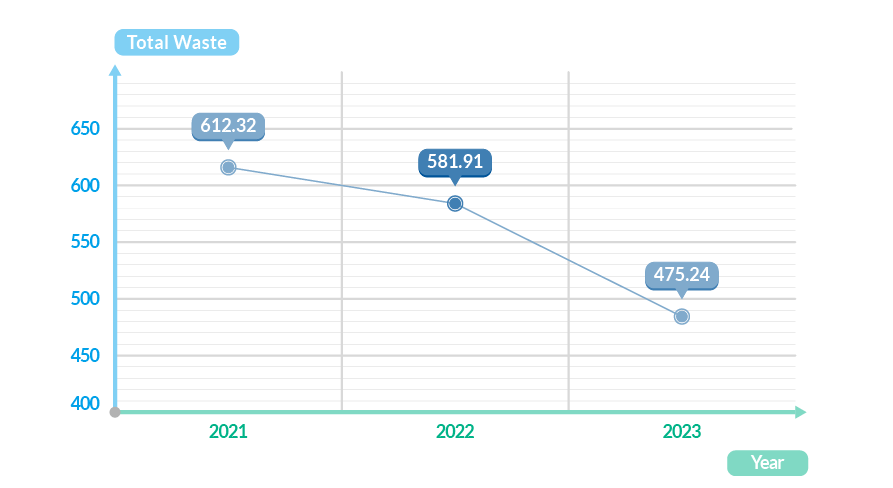