Technology and Product
Chroma started business operations with display testing, with a vision to develop precise, reliable, and unique testing instrumentation. We have gradually diversified the scope of our services to nine major testing product groups which cover power electronics, passive components, semiconductors, IC design, and others. In addition to reducing equipment energy consumption we also actively develop energy recovery equipment to fulfill the green product d emand of customers. This equipment recovers energy that is traditionally consumed in the form of heat in conventional equipment and returns it to the power grid, significantly reducing overall energy consumption. Additionally, we continuously enhance the accuracy and speed of our testing equipment, reduce product size and weight, and use innovative features to help users enhance production efficiency. All these actions demonstrate our efforts to address global warming threats as a c orporate world citizen.
Innovative technology plays a crucial role in the design of energy-efficient testing equipment. Each year we prepare a technology development roadmap based on the direction of operations. Our R&D projects are based on the principle of no repeated investment in the same technology and we coordinate all R&D units to develop different innovative technologies or enhance the performance of existing ones. Additionally, the Advanced Technology Research Center focuses on the research of core, and forward-looking technologies, to make early preparation for the requirements of new products that the Company will launch over the next 2 to 5 years. We are enhancing the rate of green equipment coverage based on a principle of the maximization of labor use.
Innovative technology plays a crucial role in the design of energy-efficient testing equipment. Each year we prepare a technology development roadmap based on the direction of operations. Our R&D projects are based on the principle of no repeated investment in the same technology and we coordinate all R&D units to develop different innovative technologies or enhance the performance of existing ones. Additionally, the Advanced Technology Research Center focuses on the research of core, and forward-looking technologies, to make early preparation for the requirements of new products that the Company will launch over the next 2 to 5 years. We are enhancing the rate of green equipment coverage based on a principle of the maximization of labor use.
Innovative technologies & Patents

Chroma allocates more than 12% of its annual revenue to research and development. This demonstrates our commitment to the development of green energy products. The Company actively fosters an innovative culture and environment, recognizes teams and individuals for their contributions to technical innovation and product performance enhancement through annual awards for innovative technologies as well as the selection of outstanding engineers. Furthermore, the Company actively seeks external sources of innovation to accelerate its technological prowess. In 2023, the Company engaged in collaborative projects with nine academic and research institutions: the National Taiwan University, National Cheng Kung University, National Taiwan University of Science and Technology, and Wayne State University in the United States. The total funding for these collaborative projects reached NT$25.85 million. Additionally, the Company hired two technical advisors to provide guidance and consultation to its R&D team.
The combined efforts of nearly 700 R&D personnel in innovative technologies resulted in applications for 53 domestic and international patents in 2023. This included 43 invention, 9 utility model, and 1 design patent. Patent applications have been filed and granted in Taiwan, China, and the United States. The increasing number of patents granted each year underscores Chroma's commitment to technological innovation and its emphasis on intellectual property rights.
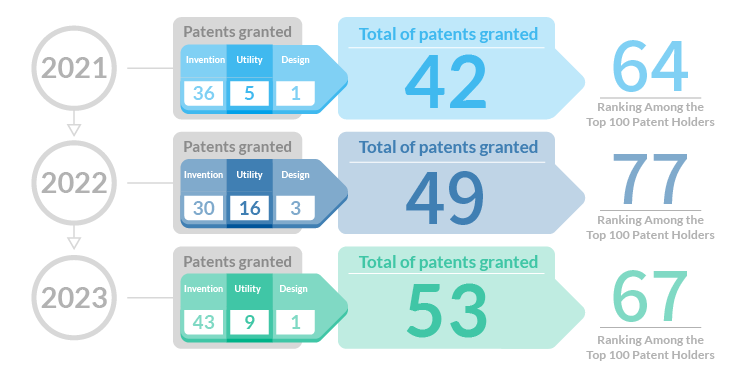
Green Chroma Label

As a provider of measurement equipment, Chroma focuses not only on its own energy saving and carbon reduction efforts but also on helping users to effectively reduce carbon emissions when using Chroma instruments in their production processes. This is precisely the concept of the carbon handprint. Based on this concept, Chroma introduced the “Green Chroma Label” system to encourage all employees to plan, develop, and produce instruments that help users reduce carbon emissions.
The Company assesses its products for the following characteristics throughout all stages of their lifecycle, including distribution and sales, product use, and waste disposal:
- Low energy consumption during use.
- Reduction of transportation and installation resources, improvement of production capacity, and reduction of customer investment costs.
- Design considerations for low noise to avoid harm to the physical and mental health of the user and finally to determine whether new products can bear the Green Chroma Label.
Products that have passed the audit will display the Green Chroma Label sticker on the back of the equipment to indicate their energy-saving effectiveness. Currently, applications for the Green Chroma Label are open to all Chroma product lines.
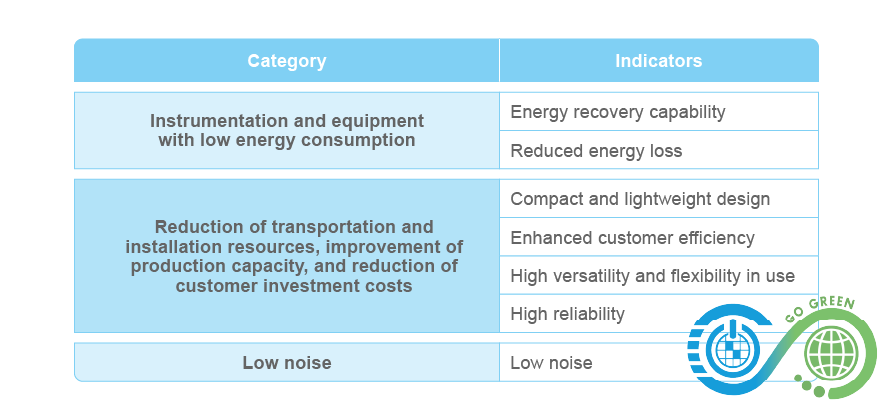
Green and Sustainable Design

Chroma demonstrate the outcome of technological innovation for outstanding performance and functionality in new products, and implement green design at all stages of the product life cycle to reduce environmental impact and realize responsible production and consumption.
The Chroma R&D unit prioritizes control and minimizes component usage, decreases energy consumption, and enhances energy efficiency in the pursuit of creating environmentally friendly, energy-efficient products:
- Component Usage Control and Reduction
We have introduced the concept of green product design in the R&D process. The relevant units are tasked with making products more energy-efficient and ensure their compliance with all the regulations on hazardous chemicals. We use renewable and recyclable materials as much as possible. Improvement and evaluation are carried out on a continuous basis to ensure that our massproduced products meet the requirements and standards of quality assurance and environmental protection.
In addition to controlling hazardous substances, the R&D unit also actively introduces circuit digitization technology to reduce the number of parts and components and promotes a shared module design philosophy for different products. The sharing of specific modules reduces the number of semi-finished products and the total number of parts and components. It also makes the launch of new products more efficient and extends green product coverage. It can also reduce energy consumption in both procurement and production. - Reduced energy loss
We continue to develop different types of technologies that can fulfill customer needs and reduce energy consumption at the same time. An example of this is energy recovery technology for electrical and electronic equipment. Energy dissipated in the form of heat is fed back into the grid as electrical energy to significantly reduce total energy consumption. This energy recovery technology is mostly used in AC/DC power supply equipment, but Chroma is using it to develop a regenerative load (sink) function, which will extend the range of application of the technology and significantly increase the overall energy recovery rate. We have also introduced a standby mode into many products. The equipment enters a Power Saving Mode when there has been no output for some time. - Enhancing Energy Efficiency
In addition to actively reducing the energy consumption of equipment itself, we also consider how to assist customers in using equipment more efficiently to further reduce energy usage. Therefore, we continue to invest in R&D resources to develop innovative technologies to improve electric energy conversion efficiency, power density, channel density, test speed, and test accuracy.
Chroma continually broadens the scope of automated testing in all manufacturing processes. This leads to a marked decrease in the need for manual testing and effectively shortens testing time. Additionally, energy recovery measures are implemented in burn-in equipment. These are coupled with intelligent control systems for data collection on energy-saving measures in burn-in chambers to reduce burn-in energy consumption.
Although testing equipment is made in small numbers there is a large variety of different units. To address the diverse production demands there is a need to build or adapt production and testing equipment. The introduction of shared modules and digital circuits allows the actual number of pieces of testing equipment to be reduced. This makes the test equipment more adaptable, and fewer and less frequent adjustments need to be made.
Although testing equipment is made in small numbers there is a large variety of different units. To address the diverse production demands there is a need to build or adapt production and testing equipment. The introduction of shared modules and digital circuits allows the actual number of pieces of testing equipment to be reduced. This makes the test equipment more adaptable, and fewer and less frequent adjustments need to be made.
The size and weight of equipment and the ease of transportation and installation are highly interrelated. We use innovative technology to reduce the size and weight of instruments and equipment, reduce the number of parts and components, and enhance the density of testing channels to maintain the same testing density as in traditional design, but in a smaller package. These measures make transportation more energy-efficient and also simplify installation. Smaller and lighter instruments and equipment are also easier to pack and transport while requiring less packaging and protective material.
Software integration and control has allowed significant improvements in the efficiency of manual operations and has reduced human error. We have also developed multifunctional equipment that allows users to make versatile combinations and reduce equipment idle time. We have actively developed intelligent devices that employ pre-diagnosis and health management technologies to give advanced notice of equipment failures. This has minimized unexpected downtime.
Chroma continually explores solutions that require less packaging material while providing proper transport protection for its instruments. Reductions in the size and weight of instruments allow the amount of packaging material and waste generated at the end of product life to be much less.
When it comes to the disposal of Chroma's packaging materials and equipment at the end of their lifespan, the responsibility lies with the user. However, all toxic and hazardous substances or elements—including lead, mercury, cadmium, hexavalent chromium, polybrominated biphenyls/polybrominated diphenyl ethers, and phthalates—in the PCBA, casing, standard accessories, and packaging materials adhere to the requirements of SJ/T 11363-2006 and EU Directives 2011/65/EU and 2015/863/EU for homogeneous materials. Detailed instructions for the disposal of equipment at the end of its life are provided in Company product manuals.
When it comes to the disposal of Chroma's packaging materials and equipment at the end of their lifespan, the responsibility lies with the user. However, all toxic and hazardous substances or elements—including lead, mercury, cadmium, hexavalent chromium, polybrominated biphenyls/polybrominated diphenyl ethers, and phthalates—in the PCBA, casing, standard accessories, and packaging materials adhere to the requirements of SJ/T 11363-2006 and EU Directives 2011/65/EU and 2015/863/EU for homogeneous materials. Detailed instructions for the disposal of equipment at the end of its life are provided in Company product manuals.
Green Design Results and Achievements
Chroma's latest energy-recovering (regenerative) DC electronic load, model 63718-1200-40, compared with the previous non-regenerative DC electronic load, model 63218A-1200-720, and the regenerative AC electronic load, model 63815R, compared with the previous non-regenerative AC electronic load, model 63804, are summarized in the table below to outline the achievements of green design. This demonstrates Chroma's active response to ESG requirements.
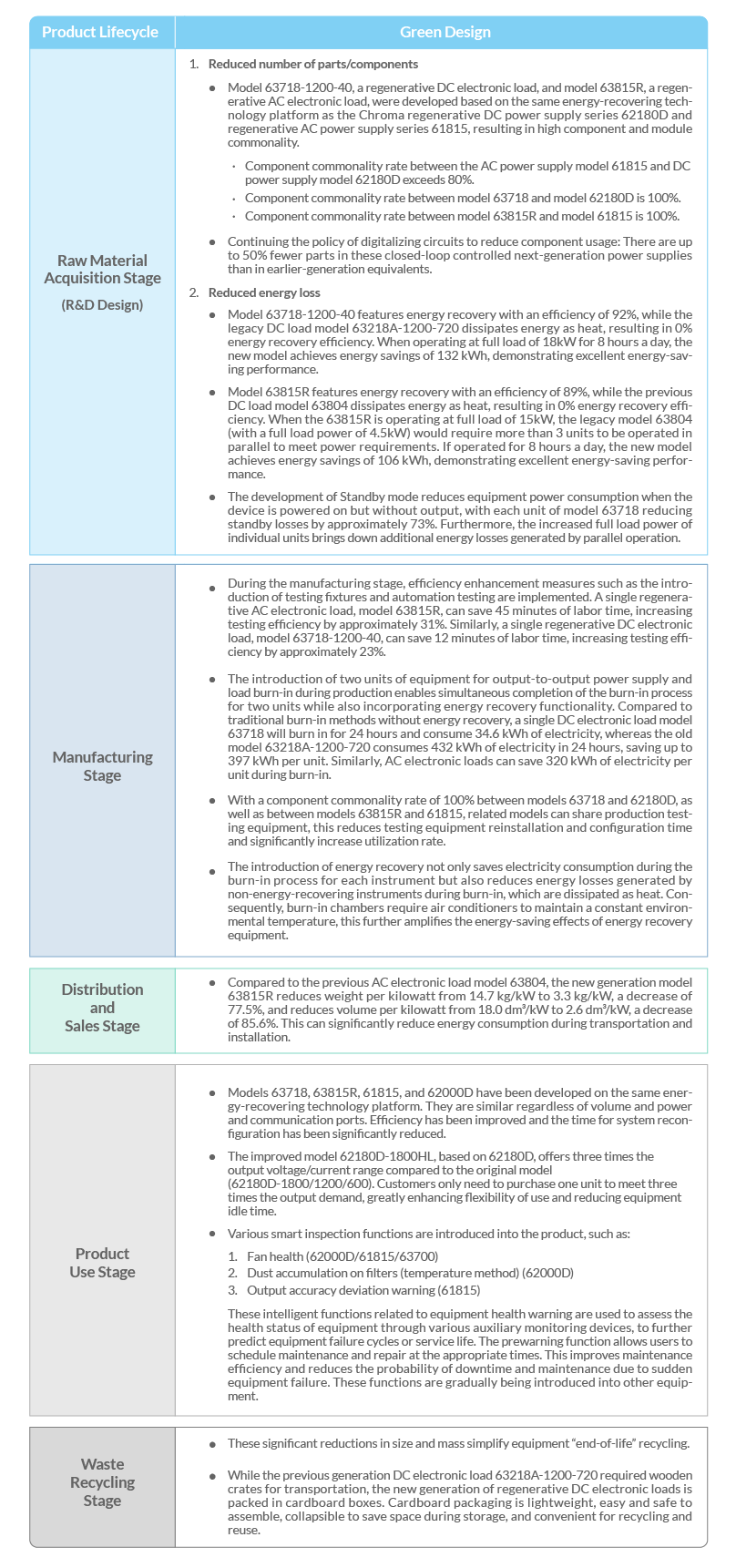
In addition to actively reducing the energy consumption of high-energy-consuming power electronic products, Chroma also addresses the energy-saving requirements of other non-power instrument equipment. The Chroma 7945 wafer inspection system is an excellent example of effective energysaving, The Chroma 7945 system is not an energy conversion device, the energy-saving strategy focuses on module sharing. This increases flexibility of use, reduces maintenance costs and increases productivity. The reduction of transportation and maintenance work also minimizes energy consumption.
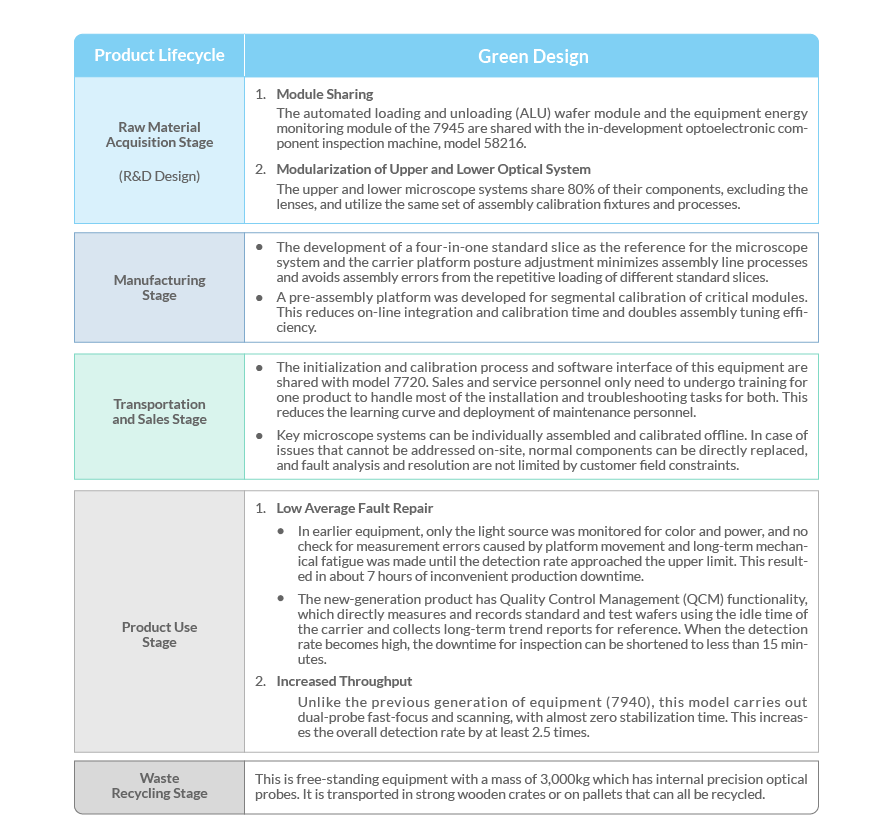
Chroma welcomes your voice, please don't hesitate to contact us!